Active Quality Control Records
Once the QCR is activated, the primary functions of the record become available. This is where the quality control workflow is executed and the QCR serves the purpose of enabling and recording the outputs of this workflow. These functions are summarized in the sections below.
Aligni’s QCR is not overly-burdened with process or stage gates in the active state. These controls are expected to be performed by personnel and not regulated by the software.
Move Inventory
In the active state, the inventory unit represented by the QCR may be moved to any other quarantine zone within the organization, even those in other warehouses. This is done manually from the QCR’s action bar.
Bin Management
Recall that a single inventory unit is attached to each QCR. An inventory unit represents some quantity of material in inventory. During the quality control process, this inventory is typically sorted in some manner to determine whether it is conforming or non-conforming to established criteria set by the organization. The process of bin management is where the inventory unit’s quantity is separated into “bins”. Each bin has incoming condition attributes, final condition attributes, and root causes representing the assessment of the inventory in that bin.
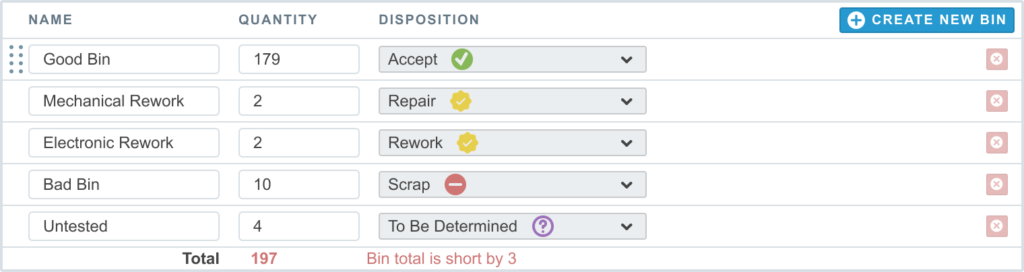
When the QCR is later closed, the inventory in each bin is then “dispositioned” to determine how the quantity in the original inventory unit is moved along within the organization. The bins are essentially provisional divisions of the QCR’s inventory as the team evaluates the material.
Active State Stages
Each organization can define multiple stages of the active state of a QCR. These stages may be helpful for imposing an organization’s own workflow sequence on the quality control process.
The stage may be changed at any time during the active state by anyone authorized to work on quality control records. How the team manages these stages is up to each organization and what their internal process is. Aligni comes pre-configured with a sensible set of stages defined, but each organization will want to review and define their own appropriate to their team, workflow, and processes.
Assessments
During the quality control process, the inventory associated with the QCR is separated into independent bins of some quantity. Each bin has its own condition assessments and root cause assessments.
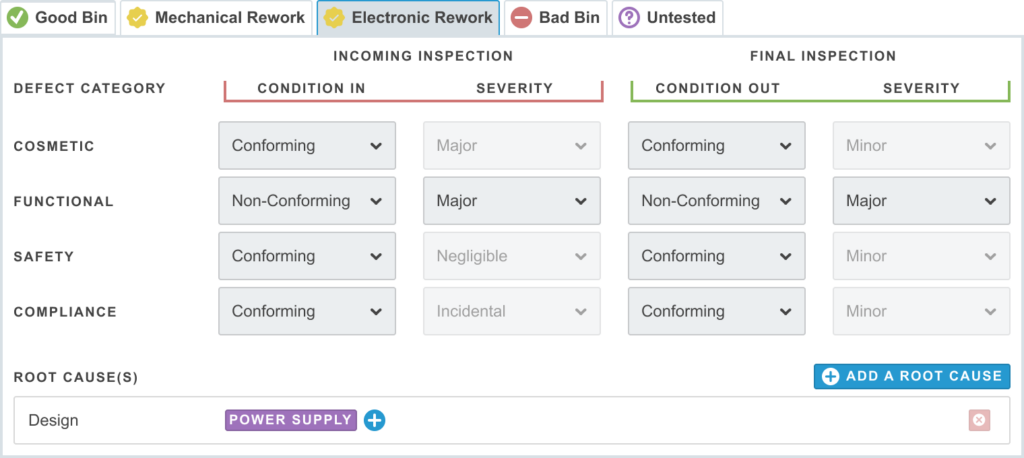
Condition assessments are available for each of the defect categories defined by your organization. Any non-conforming conditions have an additional severity attribute that is typically applied according to your organization’s handling guidelines and later used for analytics reporting. Both incoming and final inspection conditions are provided.
Root cause assessments are also available and selectable from your organization’s defined list. Within each root cause assessment, additional labels are available to define further granularity, again for handling and reporting.
Defect categories, defect severity, and root causes are managed by your organization’s owners. Root cause labels are a bit more flexible and may be managed by anyone with quality control access.
All bin management and assessments may be edited at any time in the active state except when the stage is set to Complete.
Disposition
When the stage is set to Complete, most of the bin management becomes read-only. Bin quantities and assessments are no longer editable, but the bin names and disposition may still be changed. This is the final phase before the QCR is closed.
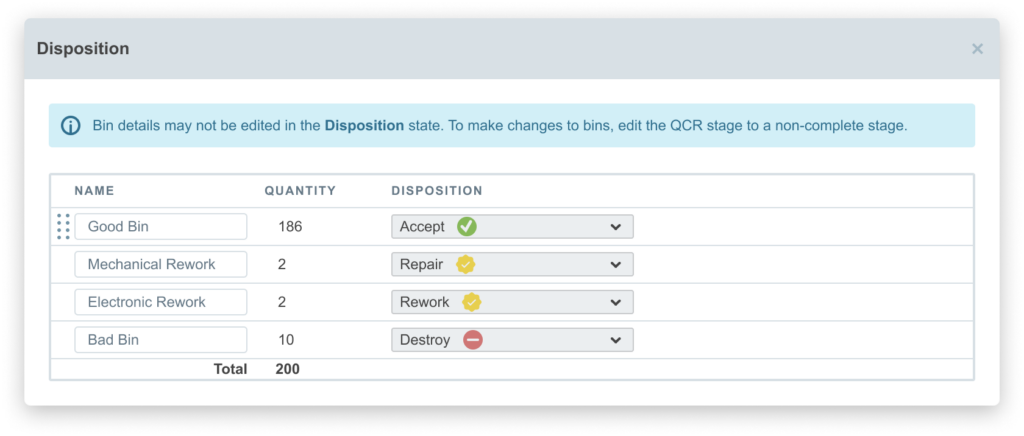
Progress and Status
Build and Purchase pages have a Quality tab to provide the current status of ongoing and completed quality control work for the associated item(s).
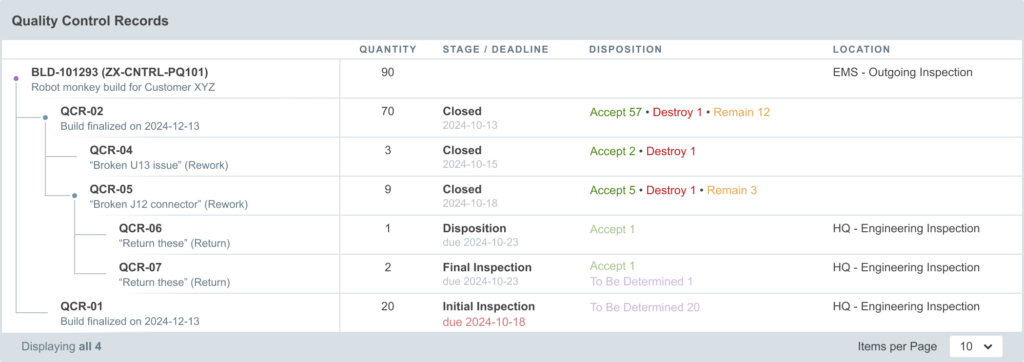
A parent-child relationship exists between QCR as the inventory makes its way through quality control. The top-level of this parent-child relationship is called the origin and is typically the build or purchase item that was sent into quality control.
When the inventory unit is split on a QCR in triage, both QCR will become children of the same source. When a QCR is closed and one or more of the bins are set to remain in quarantine, the bin itself becomes the parent of the new QCR. In this manner, a tree structure is created of all of the QCR related to the origin. This is depicted in the hierarchical view shown above.