Inventory Locations / Warehouses
Physical inventory in Aligni is represented in an inventory unit database record. This record must be associated with an inventory location (also called a warehouse) and an inventory sublocation (also called a zone). The location and sublocation are also both represented as a database record in Aligni.
A warehouse typically corresponds to a unique geographical location. However, there may be cases when an organization may want to have a single geographical location segregated for some reason and can create multiple warehouses to represent this segregation.
Certain operations and reports operate only on a single location. Notably:
- Builds – A build operates (consumes) inventory at only one location. A build may not pull inventory from multiple locations.
- Safety Stock – Safety stock limits are established separately for each location and the safety stock manager computes shortages and overages only within the context of each location separately.
Warehouse Zone Types
Warehouses are organized into multiple zones and each zone is specified as one of four types depending on the operations supported within the zone. Any number of zones may be created within a warehouse.
Standard
Standard warehouse zones behave “normally” without the exceptional behavior that other warehouse zones have. These should be used for normal operations.
Quarantine
Quarantine areas are used for quality control. Inventory may only enter quarantine areas with an accompanying quality control record (QCR). Inventory may only exit quarantine by closing the QCR.
Inventory in quarantine is non-nettable which means that it is not available for builds and will not satisfy material shortages on the material shortage report. Quarantine inventory is also not included in the “quantity available” count of an item in inventory.
Non-Nettable
Non-nettable inventory (NNI) is not available for builds and will not satisfy material shortages on the material shortage report. Non-nettable inventory is also not included in the “quantity available” count of an item in inventory.
Because the inventory is not available to builds, non-nettable inventory is also not included in on the inventory outlook chart. Furthermore, this inventory will not satisfy any safety stock requirements.
Fun fact: Non-nettable inventory is so called because it isn’t eligible to be “netted” or included in the standard calculation of available or sellable inventory. In many businesses, “netting” involves offsetting or consolidating inventory figures to arrive at a net amount of items that are ready for sale or use. Items classified as non-nettable are typically kept separate because of restrictions or issues that make them unavailable for normal operations. Examples include:
- Defective or damaged goods: Items that can’t be sold until repaired or disposed of.
- Consignment or third-party items: Stock not owned outright by the business.
- Restricted or reserved stock: Inventory held for specific purposes, quality inspections, or regulatory reasons.
- In-transit or not fully received items: Goods that haven’t yet been cleared for inclusion in the net inventory.
Vendor-Managed
Vendor-managed inventory (VMI) is inventory that is either available or not available with no corresponding quantity for the inventory. VMI has a corresponding cost per unit and can be used on builds in the traditional sense, but will never deplete. There are two common use cases for vendor-managed inventory:
- Inventory that a manufacturing partner manages outside of your organization. Components and raw materials that a contract manufacturer procures would fall into this use case.
- Commodities that your organization manages separately such as tape or adhesive or small mechanical items. In this case, you may not want to track exact quantities of the material and instead manage replenishment in a different way.
Inventory Units
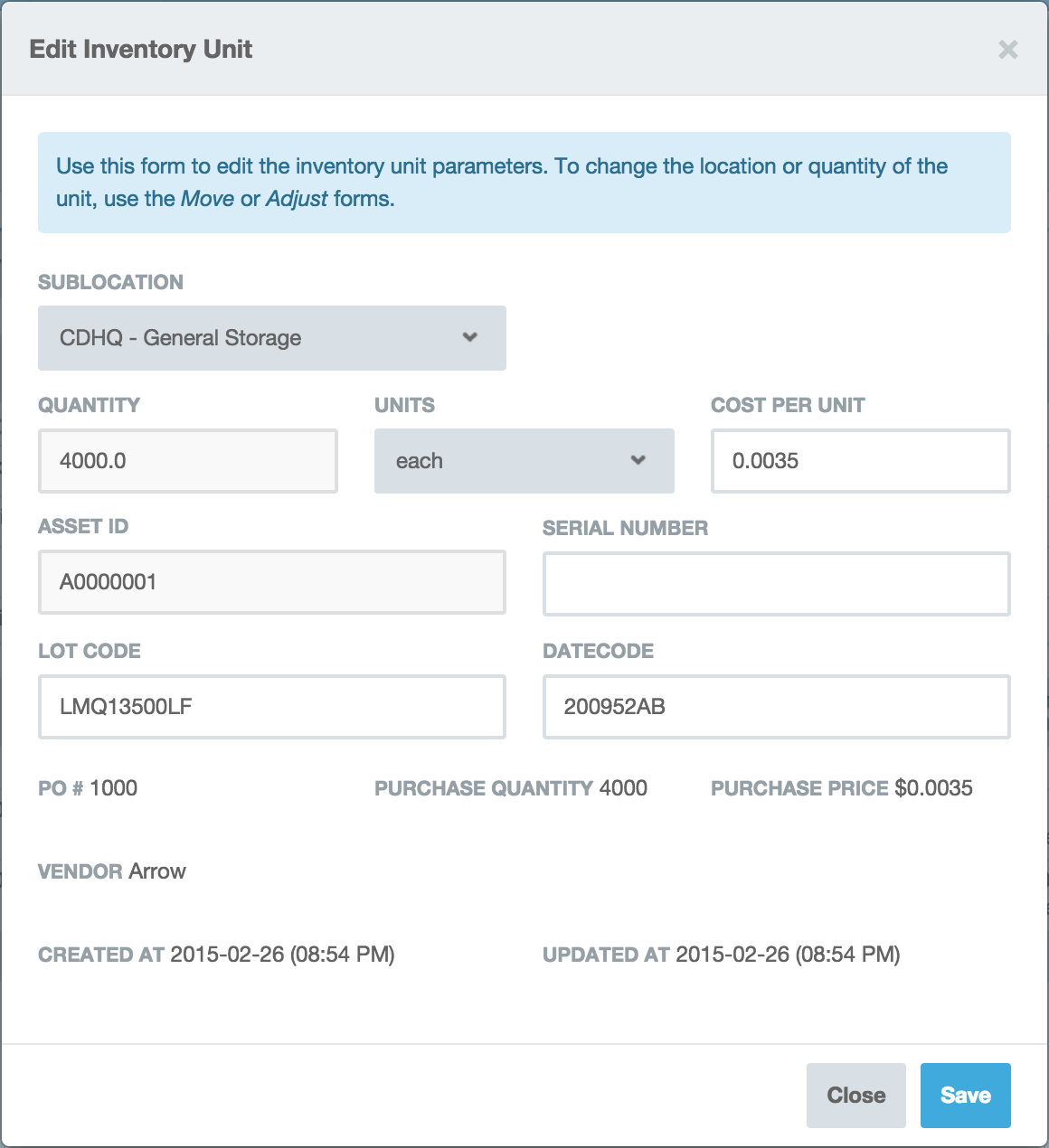
Aligni stores inventory associated with each part in entities called Inventory Units. An Inventory Unit is a single record of inventory stored at a particular inventory location/sublocation. Each inventory unit record contains the following information:
- Part – The part represented.
- Quantity – Quantity represented along with the unit of representation.
- Location – An inventory location and sublocation where the parts are stored.
- Cost – The cost per unit. (Note: the cost for the entire inventory unit would be this cost times the quantity represented.)
- Asset ID – An optional asset ID unique to each specific inventory unit.
- Serial Number – An optional serial number can be provided as long as the quantity is exactly 1.
- Lot Code – An optional lot code.
- Datecode – An optional datecode.
- Bin – When an item resides at an inventory location that supports bins, this optional string allows you to specify a bin location for the inventory.
If the inventory unit was created by receiving inventory on a purchase order, the following additional information is stored with the record:
- Purchase Order Number
- Purchase Price
- Quantity Received
- Vendor
All inventory value is recorded in the Site Currency that is established when you created your Aligni account. Inventory received on purchase orders in another currency is converted at the exchange rate specified when receiving that inventory.
The Inventory Lifecycle
One way to understand how inventory is represented in your database is to consider the inventory lifecycle – the timeline during which a physical part is represented as a database entry.
Creation
An inventory unit is created in one of two ways: manual creation from the Part Details inventory summary or by purchasing and receiving to inventory when items on a purchase order are received. Both methods generate an inventory log entry.
Transfer
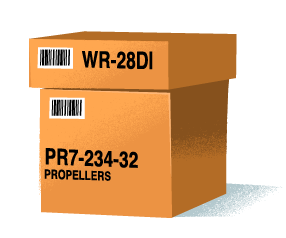
Inventory transfers are a formal method used to set aside specific inventory units and transfer them to another location, typically within a shipping and receiving context. Transfers are used to move inventory between company locations or when kitting components for contract manufacture.
Adjustment
On the inventory tab of the Part pages, users with inventory management permissions can manually adjust inventory information including cost, location, quantity, and other parameters.
Consumption
Inventory unit counts are decreased when parts are consumed on a build, either by placing them onto an assembly or, in some cases, when lost to attrition. When the entire quantity of an inventory unit is consumed, the inventory unit record itself is destroyed.
Part Inventory Summary
The Part Details page includes a compact Inventory Summary with the following information:
- Each inventory unit listed separately.
- Inventory allocated to builds, listed separately per build.
- Inventory reserved for builds, listed separately per inventory unit and build.
- Open items on purchase orders.
- Transfers in progress.
- Total and Total Available (not reserved) inventory.
Manual adjustments can also be initiated in the summary box. Click on the clock icon to see the complete inventory audit history for the part, or click on the plus icon to manually create a new inventory unit for the part.
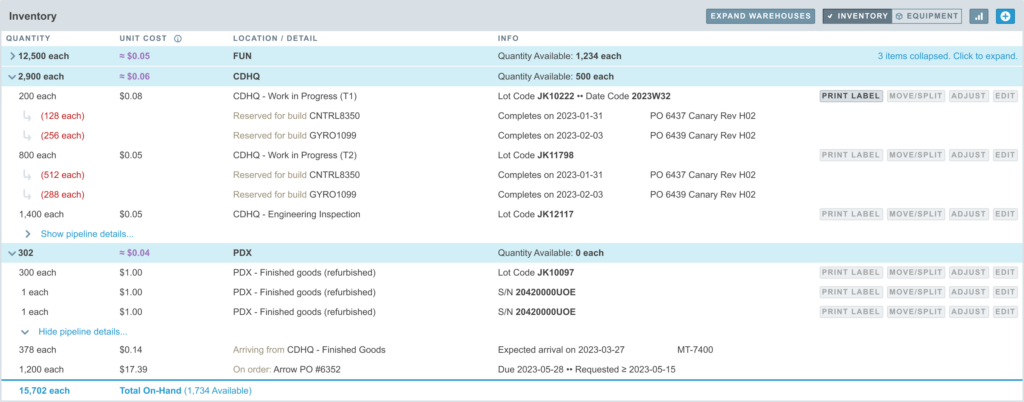
Reports
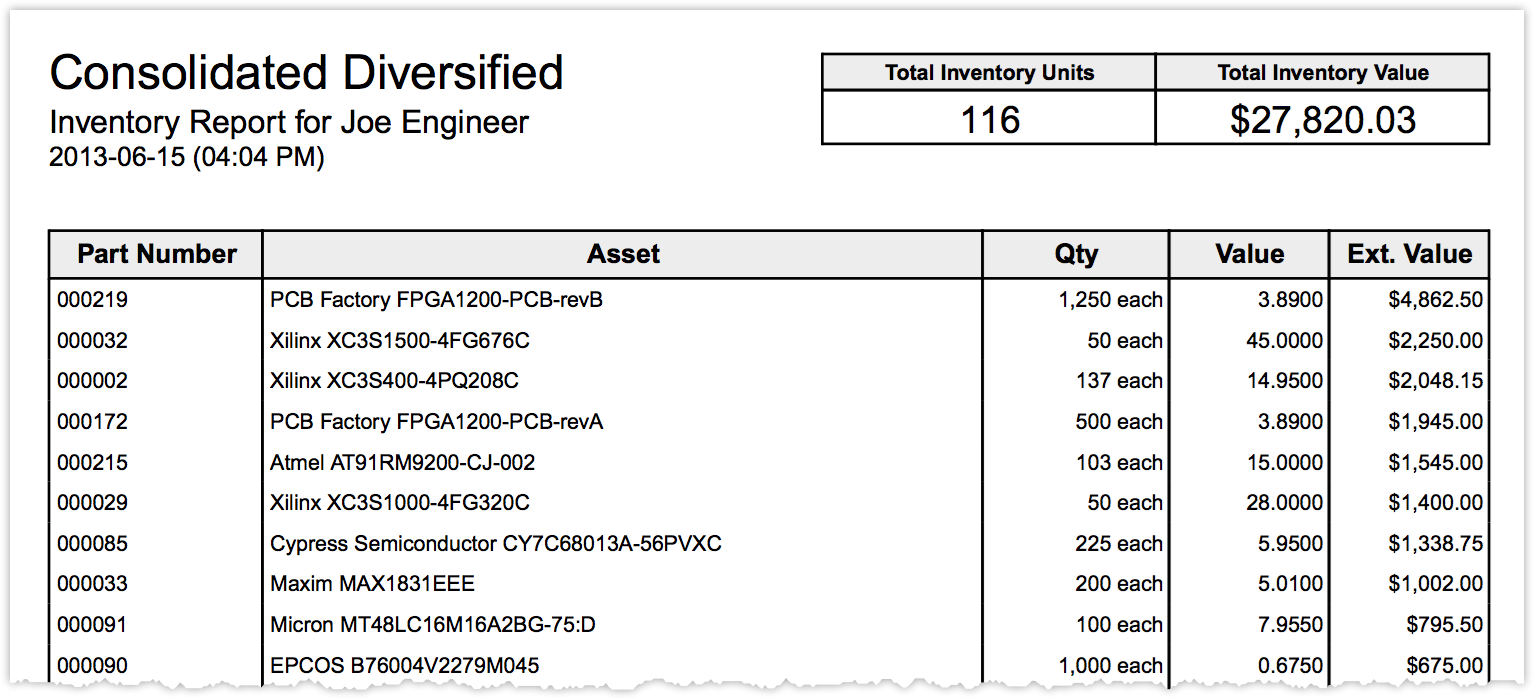
Automated inventory reports are created on the Reporting page accessible from the Inventory dashboard. Users can subscribe to one or more reports and the report will automatically be emailed to each subscribed user when it is generated.
Note that some users may not have the permissions required to receive some report configurations. If this happens, the user will be notified and unsubscribed to the report.
Inventory reports support the following options:
- Report Contents – An Adobe PDF and/or a CSV file will be attached to each inventory report email.
- Sort Style – Items on the report are sorted by value, asset ID, part number, or manufacturer P/N.
- Frequency – Reports are emailed at the end of each reporting period, either weekly, monthly, quarterly, or annually.
- Part Collection – An optional part collection may be specified to restrict the report contents to parts in the collection. When none is specified, the report will contain all parts in your database.
- Inventory Location – An optional inventory location may be specified to restrict the report contents to parts at the specified location. When none is specified, the report will contain parts at all locations.
Usage Report
You may also configure a routine usage report which includes consumption information for trailing periods (based on finalized builds as well as consumption adjustments) and forecast usage for forward-looking periods (based on allocated builds). Settings are available to define the periods and item groupings to include in the report.
Inventory Transactions
Inventory transactions are database entries created to record operations performed on inventory units. These are broken down into five different flow types:
- Inflow – This flow type indicates that inventory quantity of an item has increased and that inventory is flowing into the organization. Examples include purchases, build products, and manual creation of new inventory.
- Outflow – This flow type indicates that inventory quantity of an item has decreased and that inventory is flowing out of the organization. Consumption of inventory and sales both qualify as outflow transactions.
- Internal – This flow type indicates that the overall inventory quantity has not changed, but that inventory has moved within the organization. Transfers between warehouses or between sublocations with a warehouse would qualify as internal transactions.
- Reconcile – This flow type indicates that inventory quantity has changed, but that the flow is neither in or out. Instead, it is a reconciliation of the quantity. Examples include cycle counts or other adjustments where the previous quantity was incorrect.
- Modify – This flow type indicates that the inventory unit has been modified in some way that does not affect the total quantity of inventory. Examples include changing attributes of the inventory unit such as lot codes, date codes, or asset IDs, or the cost-per-unit. While changing the cost-per-unit may affect the inventory cost balance, it does not affect the inventory quantity.
Transaction Sources (Origins)
Each inventory transaction must originate from some process within the operation of the company. These origin sources produce different types of inventory transactions and characteristics. While these details are generally not important to the day-to-day operation of the company, it can be helpful to understand how Aligni works with the flow types above to generate certain reports and forecasts.
- Manual – Manual origins are operations that operate outside of the confines of some other process or record. These are, as the name suggests, created manually and atomically. Examples include creating a new inventory unit manually on an item’s inventory tab (inflow), manually adjusting inventory (reconcile), or updating the lot code on an inventory unit (modify).
- Purchase – When inventory is received from a purchase, the purchase is the transaction origin and the flow is inflow.
- Batch Operation – Inventory batch operations perform transactions on a collective of items and can be inflow, internal, outflow, or reconcile depending on the operation. Examples include inventory adjustment batches (cycle counts), inventory transfers, and new inventory import via CSV.
- Build – Builds generate outflow transactions for the items (components) consumed on the build and an inflow transaction for the item (assembly) produced.
- Part Revision Release – When a new part revision is released and any existing inventory is scrapped or disposed of by disposition, the reduction in inventory is an outflow transaction.
- Sale – Items consumed or sold through the sales process (such as integration with sales systems) generate outflow transactions.
- Equipment – Outflow transactions are used to take inventory out of inventory to place them into equipment – either during creation or logbook entries during the maintenance of the equipment. Similarly if an item is taken off of the equipment and put back into inventory, this is an inflow transaction.
Importing Inventory
You can import inventory units from a CSV file (spreadsheet export) from the inventory dashboard. This step is typically only performed when migrating existing data into Aligni. Under normal operations, inventory units are created by receiving items on a purchase order.
The import tool will guide you through the process:
- Download a CSV template. This template assures that the data is compatible with the import tool. You can populate this template with the data you have from some other system. Some manipulation of the data may be required to fit the template.
- Upload the CSV populated file.
- Preview the inventory units.
- Commit the changes. This final step will create the inventory units in Aligni.