Build Process
Every build is a four-step process that starts with setting up the build assembly and parameters (planning stage) and ends with inventory counts being updated and committed (commit stage).
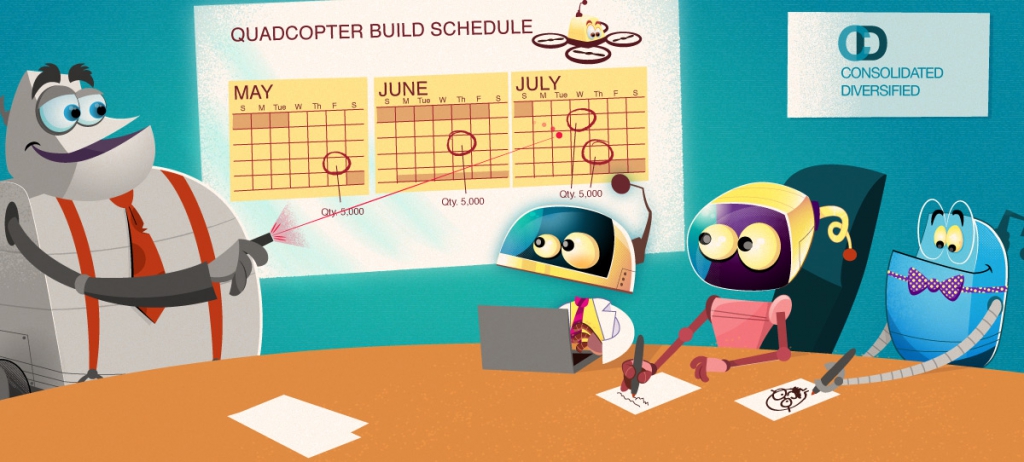
1. Schedule
Schedule a single, one-time build or multiple recurring builds, specifying the assembly part number and quantity to be built.
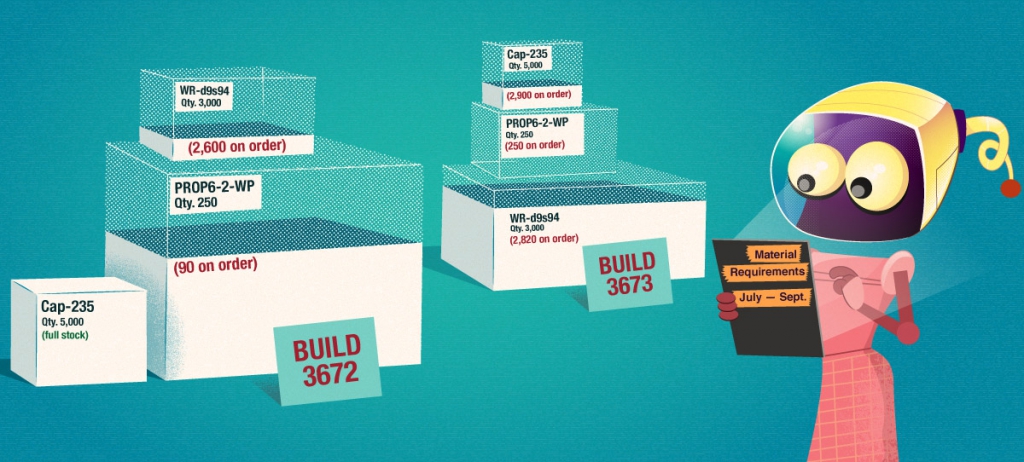
2. Allocate
Allocate parts and quantities to be consumed for the build for resource planning purposes.
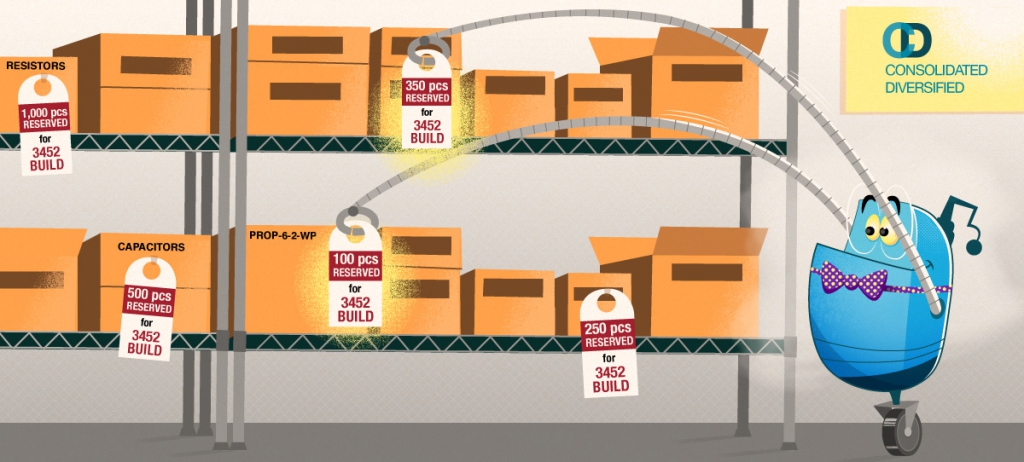
3. Reserve
When the actual assembly begins, reserve specific inventory units to make them unavailable for inventory transfers or other adjustments.
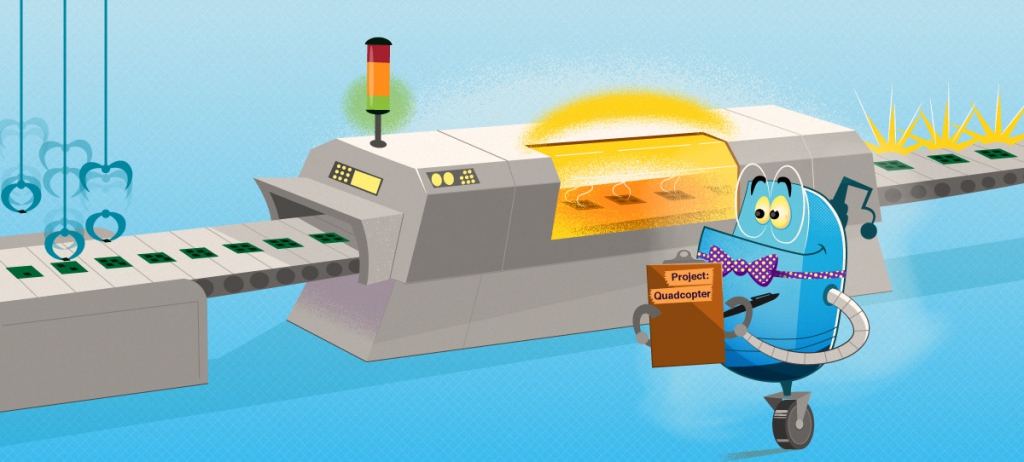
4. Finalize
Finalize the build and Aligni makes all final adjustments to the component inventory and optionally adds the finished good to inventory.
Build Manager
The build manager is displayed on your Aligni welcome page in the Supply Chain perspective. In the list mode, it provides an at-a-glance view of all current planned, scheduled, allocated, and reserved builds along with pertinent information about each build.
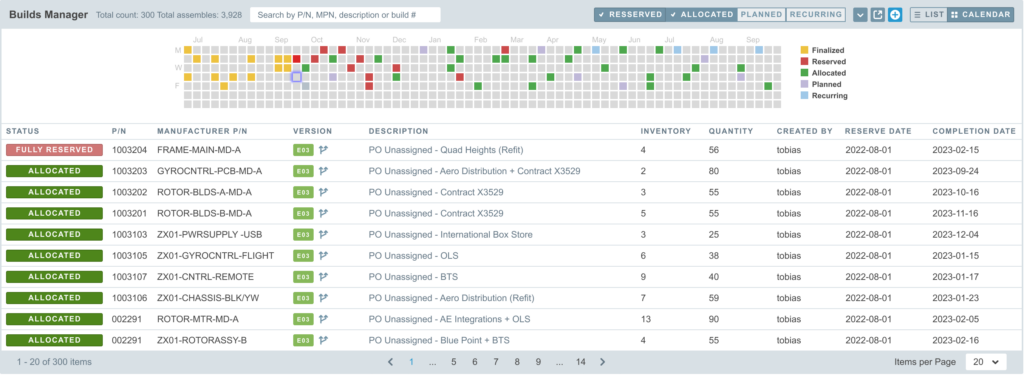
Additionally, a graphical calendar view of the build schedule is shown above the list of current builds. Place the mouse cursor over any of the calendar days and Aligni will highlight the corresponding builds in the list. Similarly, you can place the mouse cursor over any of the builds in the list and Aligni will highlight the corresponding date(s) in the calendar depiction.
Production Schedule (Calendar Mode)
In calendar mode, the build manager offers a forecast view of the inventory status and production schedule organized by product.
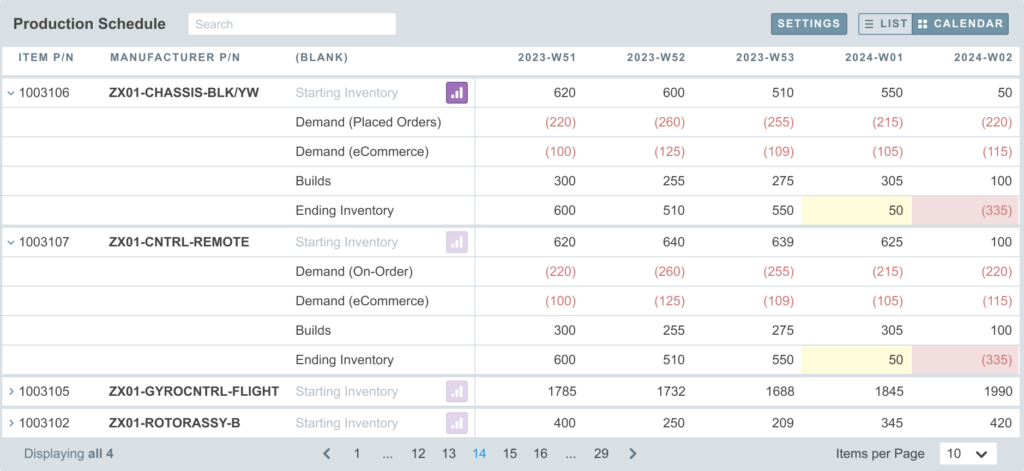
Production schedule mode is configuration through the settings button with the following options:
- Part Collection – The items that are shown on the calendar mode are determined by the selected part collection. To create and manage your part collections, visit the Aligni Home Dashboard and click on Part Collections in the Item Master area.
- Warehouses – Select which warehouses to consider for inventory visibility. Inventory and demand are pooled from the selected location and aggregated in the table.
- Interval – Select the interval (week, month, or quarter) and number of intervals to determine the columns in the table.
- Demand Thresholds – Outgoing inventory in each period is forecast by the demand estimates you’ve provided. For more information, visit the Demand Estimator documentation and the Demand Estimator guide. Demand estimates below the lowest listed prominence are not included in the production calendar forecast.
Example
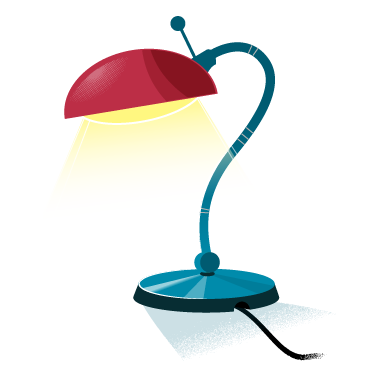
As an example, we’ll go through the build process for the ASSY_TESTUNITS assembly in the demo database. You can see the partlist at this link. This assembly is composed of the following:
- 3 each of a capacitor C0402C104K8PACTU
- 3.5 inches of wire
- 4 2-pin headers which a broken off from a separable strip of 40-pins or 80-pins
The example illustrates how Aligni handles units through the build process. The wire is specified in use-as units of inch but typically purchased on a 100-ft spool. The spool is held in inventory as fractional units, so 1 100-ft spool would mean 1,200 inches are available. 0.25 100-ft spool would mean 300 inches are available. Inches may also be specified as a fraction.
The 2-pin unit is a base unit and is integer-only. It is setup to convert to 40-pin strip and 80-pin strip since these headers are typically purchased as separable strips.