
The Material Requirements Planning (MRP) workflow is the term we use to describe the complete (and often complex) process from customer demand (a customer would like to buy your product) to finished goods.
From identifying customer demand (either make-to-order or make-to-stock) through final assembly and delivery to the customer, the MRP workflow is operated on continually in most organizations and comprises several steps that are often always in some state of progress.
While MRP software typically provides most, if not all, of the tools required to execute this system, Aligni’s material shortage report stands out as one of the most usable and robust of its kind. A solid understanding of how this tool fits into the MRP workflow will help you operate efficiently and precisely.
Production Demand
Everything starts with demand for a product you sell. Depending on the lifecycle stage of the product, this demand could be prospective or responsive. For example, if you’re working on a new product introduction (NPI), you may be working with forecast demand for the product based on how similar products have sold. If the product is mature, demand can be determined from past performance or existing customer pipeline orders. In either case, prospective or responsive demand is what drives and triggers MRP flow.
Customer and Channel Demand
Aligni’s demand estimator is where you can record, maintain, and monitor customer demand, either by specific customers and opportunities or by channel.
Make-to-Order Demand
In industries where demand is driven by specific customer orders, jobs are often dispatched as make-to-order without the intention of maintaining off-the-shelf inventory. In this case, demand estimates and builds are typically customer-specific an are created directly in response to a customer purchase order.
Make-to-Stock Demand
For make-to-stock operations such as those that regularly keep stock on hand for off-the-shelf sales, another source of production demand is safety stock. Aligni’s safety stock manager allows companies to set and maintain safety stock levels for each product (and component!) in order to assure product availability. Safety stock levels are depicted on inventory outlooks such as the one shown below.
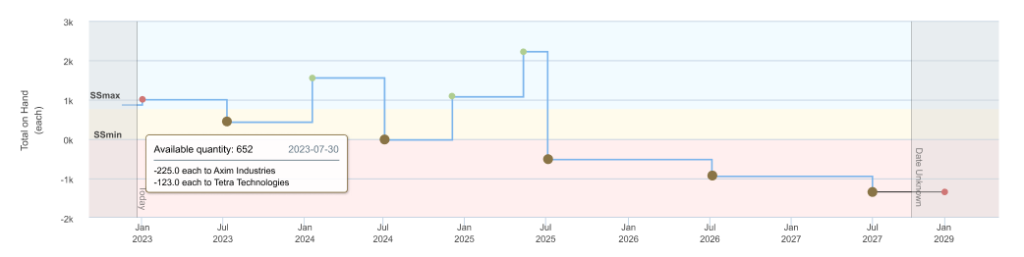
Create a Build
Within Aligni, you can represent this demand by using Planned and Scheduled Builds. Planned and scheduled builds are not actionable — that is, they don’t affect inventory or immediately trigger purchasing activities. Instead, they are representative of demand and can be used by buyers to get perspective on how demand for the product and its components will look.
A build is the workflow representing the process of assembling or manufacturing a product from various components or raw materials.
The build record itself serves several purposes. Among them are:
- Documenting the progress of the process through various stages to completion;
- Resource allocation; and
- Improving operational efficiency through clear internal and external communication.
Even though this component demand is not actionable, it is represented in the forecast part usage shown on a part’s Inventory and Supply Chain tabs for informational purposes to help guide planning.
In the example below, historical part usage is shown in yellow. Forecast usage is shown in blue based on planned or scheduled builds:

Allocate the Build
At some point, a planned build will become imminent. This timing is determined by several factors that are industry-, organization-, and product-specific. For example,
- Current product inventory
- Required safety stock
- Lead time for components and assembly activities
- Sales rate
- Cost of the product (and sensitivity to shelf inventory)
Once it has been determined that the build should proceed, the build is allocated. This is an important milestone because the build allocation generates demand for the components required on the assembly. This demand is then visible on the inventory tab for each required component. If inventory is not available, then the demand is listed on the material shortage report.
Put another way, build allocation kicks off the build process and starts the clock. In general,
Allocation Date + Time to RFQ + Component Lead Time + Time to Build = Build Completion Date
Review Material Shortages
The allocated builds generate demand and the Material Shortage Report is used to navigate and visualize these shortages. This report is highly customizable to suit particular workflows and works with the Part Cart to help buyer/planners create quotes and purchases quickly and easily.
The integrity of your production schedule relies directly on the ability of buyer/planners to identify and resolve material shortages efficiently and with a high level of confidence. When production is in full swing with dozens of assemblies, thousands of parts, and a time horizon of several months, it’s important to have flexibility in the tool that presents these shortages.
Here are several tactical approaches you may take to review the complexity of the MSR. Which tactics your team employs depends on your industry and business and the nature of supply chain management within that context. Additionally, the tactics may change as your operating environment changes.
Filtering Items
Monitoring hundreds of parts can be a bit overwhelming so reducing the observation set can be very helpful to maintaining focus and breaking down the planning problem into smaller pieces. Aligni’s MSR allows you to filter by part type (e.g. capacitors, resistors, fuses), manufacturer, or build / batch title. By organizing your approach in these dimensions, there are efficiencies that pay off as you chip away at the problem. Use creative build titles to quickly find subsets of builds that are critical, imminent, or otherwise categorical.
Build Sequences
In the Build Timeline mode, the MSR presents builds in chronological order by expected reservation (i.e. start date). This mode offers you the granularity of seeing specific builds in each column so you can solve imminent problems quickly with laser-guided accuracy.
Further refine this approach by only looking at builds within a specified time range. Using this approach, you can focus your sights on builds that might fall within a certain time frame of lead time.
Calendar Mode / Production Schedule
In Calendar Mode, the MSR collects all builds that fall within a specified period (week, month, or quarter) and puts their requirements in the same column. This softens the view from the build timeline’s granularity into something more time-based. This mode is most useful if you have reliable standard lead times maintained in your item master and you enable the “Sort by order date” option.
With “sort by order date” enabled, items are arranged top to bottom with those that must be ordered first (earliest in time) to satisfy the requirement(s). Operating this way lets you focus on the items that require the most critical attention. With a dependable production calendar, proper maintenance, and a reliable supplier network, you can use this mode to place scheduled orders to approach just-in-time manufacturing goals and reduce inventory holding costs.
Request for Quote and Purchase
With component demand, the next step is to determine where to purchase the components, how much each will cost, and when they can ship. Supplier quotes feed directly into the purchasing activities and are an important aspect of how you relate to and communicate with your suppliers. It’s particularly valuable that Aligni coordinates quoting and purchasing within the same database as your item master and demand system (builds). This reduces confusion and data entry errors passing this information to a separate system.
Receive & Reserve Inventory
Received inventory from your suppliers satisfies the component demand that was generated by builds. You may choose to reserve inventory as it arrives as a way to earmark that inventory. This prevents the inventory from being moved, adjusted, or consumed for any other build.
Once all inventory has been accounted for, the build may proceed. The lifecycle of the build allocation and reserve phases can be anywhere from a few minutes to several months depending on the organization and industry conventions.
Finalize the Build
Whether you place the assembly order as a work order internally or as a purchase order to a contract manufacturer, some action must be triggered to initiate a build. This action is often triggered by the full reservation of the build. The material requirements for the build are a requisite condition to actually performing the build. The workflow proceeds only when the appropriate personnel have completed the build.
Build finalization is the ultimate goal. The build inputs (components) are removed from inventory and the build output (finished good) is placed into inventory. The new finished goods inventory satisfies the initial product demand and completes the cycle.
Determining Assembly Cost
During the finalization process, Aligni presents the final assembly cost ledger with an opportunity to adjust the cost of non-material items such as labor, testing, etc. Material costs, non-material costs, and cost of vendor-managed items are included in the computed cost total.
Creating the Finished Goods Inventory
When the build is finalized, component inventory will be consumed and a finished goods inventory unit will be created to represent the build output. The inventory cost of this item may be derived from the computed cost (above), the standard cost, or a manual entry. If quality control is required for the item, the inventory will be created in a quarantine location and a new Quality Control Record will be created in triage.